在現(xiàn)代制造業(yè)中,壓鑄件作為一種重要的零部件,廣泛應用于汽車、航空航天、電子、醫(yī)療器械等多個領域。壓鑄件的質量直接關系到產品的性能、安全性和使用壽命,因此對其內部缺陷的檢測顯得尤為重要。在眾多無損檢測技術中,X射線檢測技術以其高效、準確、非破壞性的特點,成為壓鑄件質量檢測的方法之一。本文將深入探討壓鑄件X射線檢測儀的工作原理、應用優(yōu)勢、操作流程及未來發(fā)展趨勢,旨在為讀者提供一個全面而深入的了解。
一、工作原理
壓鑄件X射線檢測儀利用X射線的高穿透性,通過發(fā)射X射線束穿透被檢壓鑄件,X射線在穿透過程中會與物質發(fā)生相互作用,如吸收、散射等,這些相互作用導致X射線強度的衰減。壓鑄件內部如果存在氣孔、裂紋、夾雜物等缺陷,這些區(qū)域的密度與周圍組織存在差異,從而影響了X射線的透過率。檢測儀中的探測器接收穿透后的X射線,并將其轉換為電信號,經過計算機處理后形成灰度圖像,即X射線底片或數(shù)字圖像。檢測人員通過觀察這些圖像,可以直觀地發(fā)現(xiàn)壓鑄件內部的缺陷位置和形態(tài)。
二、應用優(yōu)勢
1. 高精度檢測:X射線檢測技術能夠檢測到微米級別的缺陷,確保壓鑄件的質量符合高標準要求。
2. 非破壞性:相較于破壞性測試,X射線檢測不會對壓鑄件造成物理損傷,適用于批量生產和在線檢測。
3. 全面覆蓋:可對壓鑄件進行100%的體積檢測,不受形狀、尺寸限制,有效避免漏檢。
4. 高效快捷:隨著技術的發(fā)展,現(xiàn)代X射線檢測設備自動化程度高,檢測速度快,大幅提高了生產效率。
5. 數(shù)據(jù)存儲與分析:數(shù)字化圖像便于存儲、傳輸和遠程分析,有利于建立質量追溯體系,優(yōu)化生產工藝。
三、操作流程
1. 準備階段:根據(jù)壓鑄件的材質、厚度和預期檢測目標,選擇合適的X射線源和檢測參數(shù)(如電壓、電流)。同時,確保檢測區(qū)域的安全防護措施到位,避免X射線泄漏對人員造成傷害。
2. 放置樣品:將壓鑄件放置于檢測儀的工作臺上,確保樣品穩(wěn)定且位置正確,以便獲取較佳的檢測效果。
3. 執(zhí)行檢測:啟動檢測程序,X射線源發(fā)射X射線,探測器接收信號并轉化為圖像數(shù)據(jù)。此過程可能需要調整焦距、曝光時間等參數(shù)以獲得較佳圖像質量。
4. 圖像分析:檢測完成后,通過軟件對獲取的X射線圖像進行分析,識別并記錄缺陷信息。必要時,可采用圖像增強、三維重建等技術輔助判斷。
5. 報告生成:根據(jù)分析結果,編制詳細的檢測報告,包括檢測日期、壓鑄件編號、缺陷位置、大小及類型等信息,為后續(xù)的質量控制和工藝改進提供依據(jù)。
四、未來發(fā)展趨勢
隨著智能制造和工業(yè)互聯(lián)網的快速發(fā)展,壓鑄件X射線檢測儀正向著更高分辨率、更快檢測速度、更智能化方向發(fā)展。具體而言:
1、技術融合:結合人工智能、機器學習算法,提高缺陷識別的準確性和效率,實現(xiàn)自動或半自動缺陷分類和評估。
2、三維成像技術:采用CT(計算機斷層掃描)技術,獲取壓鑄件內部的三維結構信息,提供更全面的缺陷分析。
3、遠程監(jiān)控與維護:通過物聯(lián)網技術,實現(xiàn)設備的遠程監(jiān)控、故障診斷和預防性維護,降低運營成本。
4、環(huán)保節(jié)能:研發(fā)低劑量X射線源和高效能量回收系統(tǒng),減少對環(huán)境的影響,符合綠色制造理念。
綜上所述,壓鑄件X射線檢測儀作為現(xiàn)代工業(yè)質量控制的重要工具,不僅確保了產品質量,推動了技術創(chuàng)新,還促進了制造業(yè)的可持續(xù)發(fā)展。隨著技術的不斷進步,其在未來制造業(yè)中的應用前景將更加廣闊。
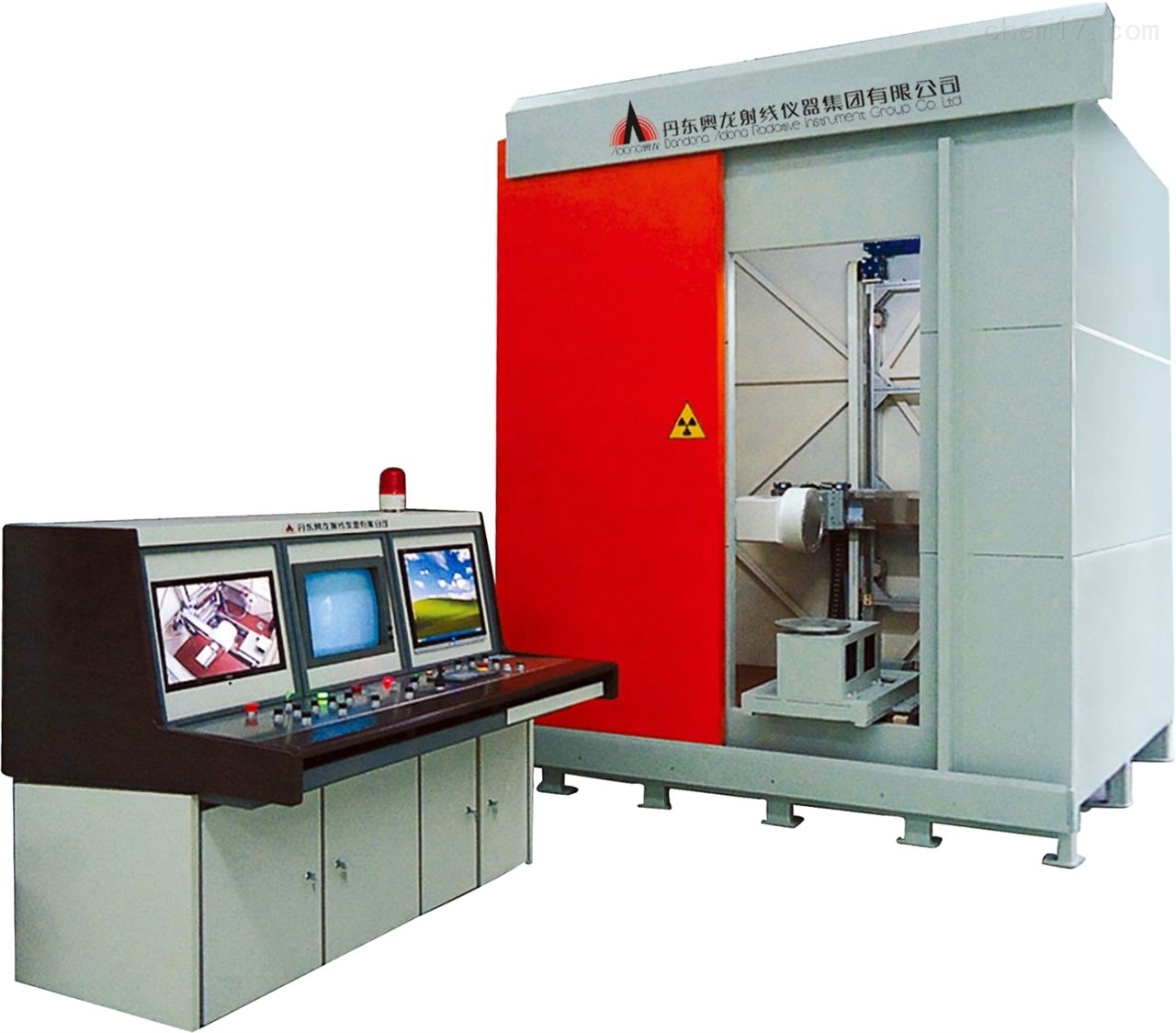